Plastic Extrusion: The Building Blocks of Today and Tomorrow
Ever wondered why plastic products are numbered in the millions and found everywhere? Take low cost and fast production times for starters, paired with exceptional durability and flexibility, and the fact that the materials are lightweight, versatile and easy to handle and transport.
Production processes are also relatively straightforward and good for high-volume turnover. It ranges from injection moulding in automotive parts and consumer electronics, thermoforming in bins, trays and sporting goods and extrusion in window frames, doors and wire insulation.
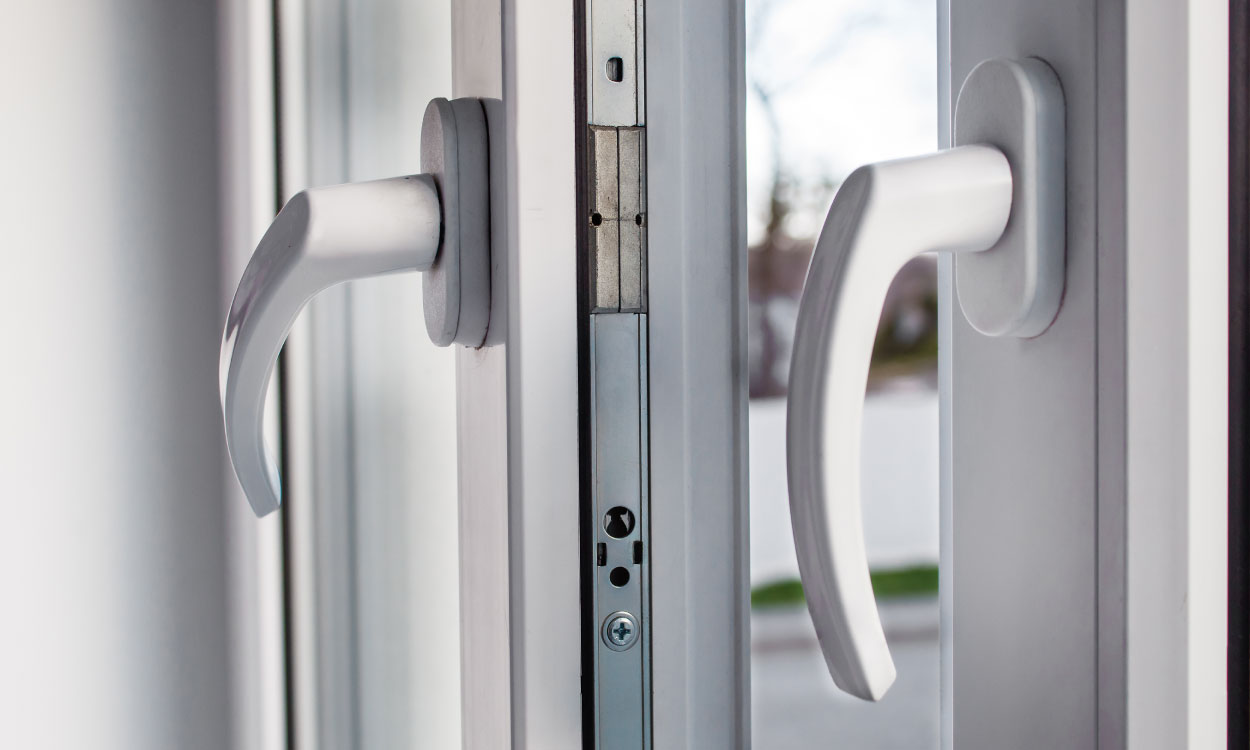
The Basics of Plastic Extrusion
Plastic extrusion is one of the more widespread plastic manufacturing processes. It’s existed for nearly a century and remained virtually unchanged. Extruding involves pushing granulated plastic particles through an extruder that heats and pressurises the molten material through different sections of the extruder and shapes it into distinct profiles using dies. It is then cooled and solidified into the desired shape.
A more detailed description is that granulated raw materials or polymers are first fed into a hopper. This granulated mix drops through a feed throat by way of gravity and onto a barrel for further processing. The barrel heats the material, and temperatures steadily rise as it is pushed through the machine by way of a rotating screw.
Along with rising temperatures, the pressure acting on the heated plastic increases as the screw thread decreases. When the plastic has reached the end of the screw it is filtered of contaminants in a screen pack, then pushed through a die. This is what gives the end product its final shape and profile. After being pulled through the die, the plastic is cooled and takes on a permanent, solid form.
Types of Plastic Extrusion Processes
The die determines shapes and profiles and leads to different extrusion processes in which varied plastic extrusions are formed. This ranges from pipes and tubes produced with tubing extrusion and everyday products such as shopping bags, wraps and packaging made using blown film extrusion.
Sheet film extrusion is similar but produces plastic items that are thicker such as cups and utensils. And insulation sheaths in wires are made with a process called over-jacket extrusion.
- Tubing Extrusion – tubes and pipes are formed with air and positive air pressure. Common items produced this way are PVC water and sewer pipes of varying diameters (some exceeding 150cm/60 inches in diameter) to exceptionally detailed medical tubes measuring a minute 0.01 inches/0.025cm.
- Blown Film Extrusion – this is used in the production of plastic film tubes through continuous sheeting. The melted film tube is cooled inside the extruder before leaving the die. creating a semi-solid tube which is then blown to the desired shape, size and thickness.
- Sheet Extrusion – involves plastic sheeting that is too thick to be blown but instead is pulled out of the die and cooled with a system of cooling rollers which determine the end-products thickness.
- Jacket Extrusion involves wire being pulled through the die and insulation extruded around it. Adhesion can be added by using pressure tooling with molten plastic added while the wire is still in the die. Uncoated insulation is achieved with jacket tooling and molten plastic added to the wire as it exits the die.
Main Advantages
This is one of the main ways that a wide variety of plastic products are produced. The process has several advantages:
- Cost-Effective – Extrusion doesn’t require expensive tooling, meaning lower initial and production costs. Machines can additionally operate continuously, effectively reducing downtime.
- Flexibility and Eco-Friendliness – The process uses thermoplastics which are recyclable and can be heated and shaped or reshaped into any product time after time. There’s virtually no waste as materials can be reused for different purposes with minimal changes to tooling and dies. In addition, different profiles and products with complex shapes, varying thicknesses, hardness, textures and colours can be easily produced in a high-volume turnout. This is down to the fact that this material is easy to form when in a liquid state.
- Ability to Use Reinforcements, Fillers and Additives – Reinforcements such as glass and carbon fibre can be used to increase tensile and compressive strength or hardness during co-extrusion or when both materials are pushed through the die. Fillers, such as metals, minerals and other plastics are added to reduce production costs or enhance performance. And additives can be used for things like increased UV, impact and fire resistance or improve flexibility, reduce weight, increased adhesion or improve colour and resistance to fading.
Materials Used
The number of materials that can undergo extrusion is increasing by the day, and new developments have resulted in products that can rival metals, wood, rubber and other materials in more demanding settings. Choosing the right materials for your plastic extrusions boils down to a basic knowledge of their molecular structure and properties.
A large portion is so-called commodity-grade plastics seen in everyday items. Here we find polyvinyl chloride (PVC), polypropylene (PP) and polyethylene (PE) and their variations as the most common. PVC is widely used in tubing, seals, housings, gaskets, bumpers, window and door frames, gutters, cladding and trim elements, in the automotive, construction, plumbing, cabling and other industries. The material is inherently rigid, has good impact and chemical resistance and is easy to mould and modified with a range of additives (such as in flexible PVC conduit) for improved properties.
PP is very durable, and fares well against liquids, high temperatures, impact and corrosive chemicals. It is seen in weather stripping, window seals, medical instruments, tubes and other areas. PE can be either rigid or flexible, with excellent strength and good chemical and corrosion resistance. it can come in different densities leading to low-density LDPE and high-density HDPE. The material is found in items as diverse as cords, bindings, shims, chock blocks and other products.
Engineering-grade polymers used in extrusion include thermoplastic elastomers (TPEs), acrylonitrile butadiene styrene (ABS), polyamide (PA) or more commonly known as Nylon and polycarbonate (PC). TPE is used in automotive parts, hinges and expansion joints due to their good tear strength, fatigue resistance and the fact they work well against oil and grease.
ABS is a lightweight thermoplastic with high impact and mechanical strength, good electrical; properties and resistance to abrasion and moisture. It is readily used in items like trays and bins, machine guards, sporting goods, office equipment and components used in electrical appliances.
Nylon is a staple in things like screws, bolts, tubes and fittings in construction and plumbing as well as clothing, machine parts, seat covers, seat belts, parachutes etc owing to its high flexibility and durability and the fact that it is easy to work with. And lastly, the PC is used in electrical componentry and optics and is the only extruded polymer that is transparent.
All materials mentioned above are used daily in high-volume production. However, when you need the best mechanical and thermal properties, high-performance materials such as PEEK (polyether ether ketone) used in pumps, bearings piston parts, PSU (polysulfone) in medical instruments, membranes and fuel cells, and PVDF (polyvinylidene fluoride) found in chemical tank liner and semiconductors are irreplaceable options for specialised uses.
Wrapping Up
Extrusion is a common manufacturing process that’s used to make everyday items such as window frames, pipes, doors, sheeting and cleaning equipment to more specialised products like cable and wire insulation and automotive, medical and electrical parts found in dozens of industries. The process is cost-effective, relatively simple to master and offers flexibility in terms of profiles, shapes, colours and sizes. It can also be tailored to specific needs with the use of different materials.