A Guide to Custom Cut Foam in the Home
What is Foam?
Foam is a material made from various chemical compounds and used in various domestic, commercial and industrial settings. We can find foam all around us – in the home, on public transport, in cars, soft furnishings, in hospitals, within buildings as construction material, and more. Two foams you are most likely to know about include polyurethane foam – a closed-cell type of foam found in many soft furnishings and seating applications – and memory foam, a foam typically used for comfort and in medical settings that has a soft, luxurious feel.
Polyurethane foam is one of the most versatile foams on the market and is a very strong and chemically-resistant roam. Known for being rigid, lightweight, flexible and resistant to bacteria, it is suitable for all sorts of industrial and commercial uses. Polyurethane foam is found in packaging, buoyancy aids, bus and train seats, and is also used within buildings as an excellent thermal insulator.
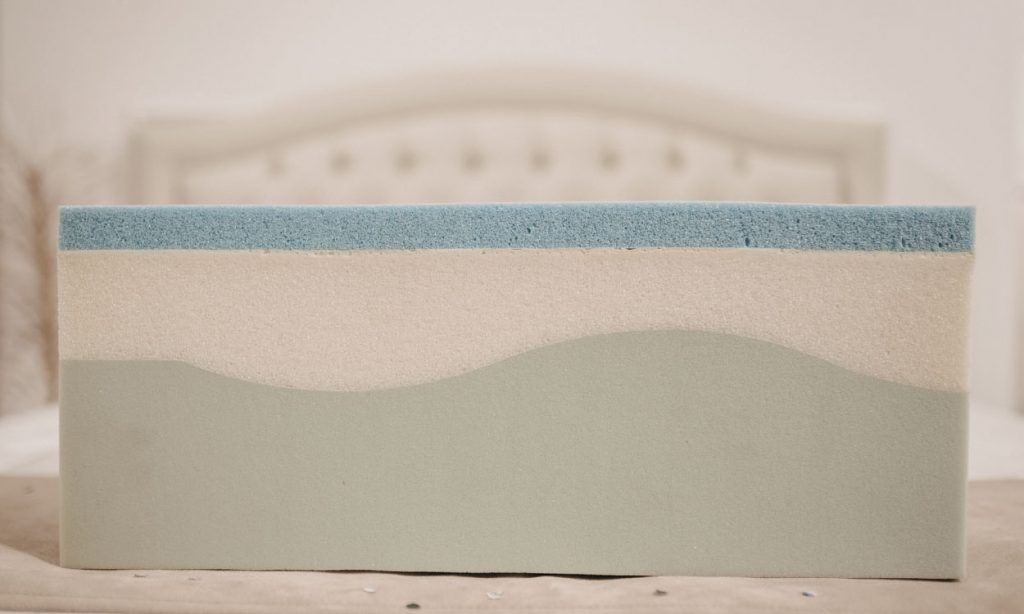
How is Foam Made?
This largely depends on the type of foam in question, as well as its desired density. Foam is created through a range of chemical reactions, and it starts off in liquid form. Once these liquid components meet, they quickly form a foam-like collection of material known as slabstock before being moulded into desired shapes and altered further to create a foam with new properties and material characteristics. Certain additives can be added to the mix to create foams with specialist properties, such as being fire retardant and waterproof.
Sometimes the foam pieces need additional shaping despite being manufactured within a mould. Using tools such as lasers, water jets, cutters, hot wires, and compression techniques, specially-shaped foams such as convoluted foam can be created. Other characteristics can be created by combining polyurethane foam with other materials and fibres in a process called reformulation. By melting or powder laminating – a process known as ‘bonding’ – a whole range of foams can be created and transformed. In other words, the possibilities are endless. All products can be made, including custom cut foam and made to measure foam.
What is Custom Foam?
Custom cut foam, also known as foam cut to size, is exactly as the name states – a totally unique foam product that has been made to a customer’s complete specification. Typical qualities often asked for include foams of a certain density, size and thickness. What’s more is that custom foam is not only limited to polyurethane foams. Acoustic foams, memory foam, aquatic foam (also known as reticulated polyether foam), and more, can all be created in any particular way. It all depends on the end application of the foam – whether that’s for a personal project, commercial application, or a larger household use. For foam cut to size and shape, customers typically approach foam manufacturers directly who supply both trade and individual customers.
Custom cut foam and others made to measure foam are very easy to order. Most manufacturers have online websites and in-built custom foam tools so that orders can be easily specified without needing to contact customer services. However for more specific requests, these manufacturers have dedicated colleagues who are able to help with all manner of asks. Don’t fret – you need not be an industrial customer or need to put in a large order to request custom cut foam.
Where is Custom Foam Used?
As we know, foams of all types, shapes, and sizes are used in a huge number of applications. Custom cut foam is a popular choice within the home, particularly for soft furnishings. For example, sofa cushions and scatter cushions come in so many designs and sizes that finding a one-size-fits-all replacement is highly unlikely. A customer would therefore approach a manufacturer with their exact measurements to order replacement foam cushions or other replacement foam parts for their sofas and soft furnishings. The same goes for items such as dining chairs – foam seat pads often need replacing, but again, finding a pre-made replacement foam of the same fit and specification is easier said than done.
In similar fashion, custom foam is also ordered for various industry applications including transport seating, components within cars, buses and trains, restaurant seating, gym floors, poolside equipment and furniture, construction projects (home insulation and soundproofing, for example) and more. The number of custom-made foam applications could go on forever.
What is the Process of Foam Cut to Size?
If you’re after foam cut to size or shape, especially for more specialist foams – like a request for memory foam cut to size – it’s best to leave it to the experts. There are many steps to creating the perfect foam product and any knowledgeable manufacturer will be willing to help, no matter how small or large your order. Ordering made to measure foam is as easy as taking your exact measurements, confirming the qualities of your chosen foam, and sending these to your chosen supplier. Most manufacturers have their own online cut to size foam tools, making the process even easier. This is great if you have a fairly standard foam shape in mind.
Most manufacturers replicate sizes and dimensions via a computer 3D model once specifications are known. If your foam piece is of an awkward shape, a to-size trace or drawing can be sent via post or email to most foam companies. In addition to size specifications, most manufacturers will want to know the intended application for the foam (so they can recommend the most suitable foam product, and if required, density) and the colour. Some foams only come in one standard colour, but this shouldn’t be an issue for most applications as it will be hidden within upholstery or another covering.
Different manufacturers use a range of cutting tools and methods depending on the intended application, density, and foam type. This can involve a range of manual tools such as specialist blades, lasers, water jets and more. Given that manufacturers are specialists in what they do, no job is too complex – they’ll usually be able to provide the best guidance and have the most suitable tools for the task!
Once your order has been confirmed, you could have it delivered to your door in a matter of a day or two. For more complex or larger projects, longer lead times could be involved but your manufacturer will confirm this with you upon order confirmation.
What is the Cost of Custom Cut Foam?
Naturally the cost of your order wholly depends on the foam you have chosen, the size, density, qualities and characteristics of the foam, and the quantity ordered. Small projects could cost as little as a few pounds, whereas large industrial projects run into the thousands. The good news is that with the range of options available in the market, you’ll be able to find the best deal for you. UK manufacturers in particular are known for their incredibly high-quality product standards, and foams manufactured in the UK are often guaranteed to be made without the use of harmful or toxic chemicals. All manufacturers will be willing to chat through a quote with you – just ask!
Buying Tips for Custom Cut Foam
Whether you’re buying foam for a personal project or an industrial application, the important thing to do is ask questions. Ask about appropriate foam types, densities, recommended characteristics, measurements and more. A good supplier will be willing to give you all the guidance you need, so do your research and get in touch.